BOSTON, May 22, 2024 /PRNewswire/ -- Technologies that
are now becoming more mainstream in the automotive industry are
also finding their way into the off-highway sector, especially
mining vehicles. In particular, IDTechEx's market research
report, "Electric Vehicles in Mining 2024-2044: Technologies,
Players, and Forecasts", highlights the role of large EV batteries
and innovative fast charging methods in driving the adoption of
electric mining vehicles, as well as the rise of autonomous mining
vehicles. IDTechEx forecasts that the electric mining vehicle
industry will be valued at nearly US$23
billion by 2044.
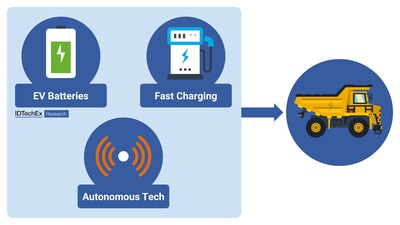
Many see electrification as the future of mining vehicles, as it
can achieve meaningful emissions reductions for the mining industry
while also being cheaper, safer, and more productive for mines to
operate. However, before these benefits can be realized, the
enabling technologies surrounding EVs must be thoroughly developed
to a point where adopting one is as painless as possible. Building
out battery and charging technology will be crucial in the
industry's electric transition.
Batteries for mining vehicles
Hydrogen fuel cells will likely be a part of the decarbonization
solution in mining vehicles, but IDTechEx expects battery-electric
to be the predominant way forward. The battery technology within an
electric mining vehicle will be critical in determining its
performance, including its endurance, lifetime, productivity, and
more. Mining vehicles come in a wide range of sizes, so mining
batteries can vary wildly too – from 100 kWh for light vehicles up
to 2 MWh for large electric haul trucks. The uniquely large nature
of these batteries means they are only now becoming sufficiently
developed and competitively priced. Turnkey battery suppliers,
including CATL, ABB, and Northvolt, have developed products that
are particularly well-suited to mining vehicles, and their
development work is still continuing.
NMC and LFP are the two battery chemistries that have so far
seen use in mining. IDTechEx's analysis shows that most mining EVs
(just under 80%) use LFP, and this is due to the specific
priorities of the vehicles. LFP tends to have lower energy
densities than NMC, but this is not a major concern for mining
vehicles – which are typically already heavy and will carry
additional loads of ore on top of that.
Where LFP does win out is in its cycle life. IDTechEx expects
that some of the most demanding mining vehicles, such as haul
trucks, will far exceed the cycle life deliverable by a single NMC
or LFP pack and require multiple battery replacements. Minimizing
the frequency of replacements by using a longer-life battery pack
is an effective way to make EVs more economical. Safety is another
crucial factor in mining, especially regarding the fire safety of
batteries in underground tunnels. LFP cells are generally
considered safer in this aspect, which limits the risk posed to
mine workers.
Looking beyond NMC and LFP, IDTechEx expects more battery
technologies such as LTO and Na-ion to continue developing and
eventually see viability for mining vehicles. The use of these
technologies will rely on how well they can satisfy the particular
needs of vehicles.
Fast charging
The challenge of vehicle charging is one of the central barriers
to the adoption of mining EVs. Where mines are used to the fast
refueling of vehicles in 10 to 20 minutes, charging usually takes
multiple hours of downtime and hinders the vehicle's productivity.
To combat this, OEMs are working on a variety of innovative
solutions to bring downtimes closer to a level that mines are more
familiar with.
Conventional cable-based charging methods are used in many of
these solutions, with most mining EVs utilizing DC fast charging.
OEMs are now looking to employ methods including multi-gun charging
and megawatt charging systems to bring times down to between 20 and
60 minutes (or 1 to 3C). This goes some way to increasing the
productivity of vehicles, but charging at such high rates can
accelerate the degradation of batteries and increase the frequency
of battery replacements.
Battery swapping is an alternative to cable-based charging,
which has seen a lot of interest from mining OEMs, particularly for
underground vehicles. This involves having two swappable battery
packs per vehicle, one of which can be charged while the other is
used in operation. Swapping is done in dedicated swapping stations
using a crane or hoist in as little as 5 to 10 minutes – making it
even faster than even conventional diesel refueling. Battery
swapping is excellent for productivity but can be more expensive in
some scenarios and will require dedicated space and infrastructure
for swapping.
Dynamic charging also plays a role in mining – vehicles can be
charged in-cycle using power rails or overhead catenary lines along
major pathways. This has the potential to completely eliminate
charging downtime and maximize productivity, but it is still being
developed and has seen the least use.
All of the above charging methods are likely to play a part in
driving the electrification of the industry, with different methods
to be used for different vehicles depending on their technical
requirements and duty cycle demands. OEMs and charging providers
are still working on optimizing their technologies, with more
detailed analysis of each available in the IDTechEx report,
"Electric Vehicles in Mining 2024-2044: Technologies, Players, and
Forecasts".
Autonomous technology
The mining industry has historically been labor-intensive and
posed a great risk to worker safety. Vehicle drivers work long
shifts under exposure to heat and noise, which can contribute to
workplace accidents and cause injury or loss of life. The
automation of vehicles is one way for operators to minimize the
human cost of mining and improve overall safety.
The mining industry is particularly well-suited to automation
too. Most vehicles travel along the same general routes with few
intersections and limited external traffic. The road networks of a
mine represent a very narrow operational design domain for an
autonomous vehicle.
It is for these reasons that autonomous mining vehicles first
entered the market as early as the 1990s (far before electric
mining vehicles), with Caterpillar introducing them as an
additional service for their haul trucks. The use of these grew
steadily until the late 2010s before seeing an adoption boom in the
last 5 years – jumping from around 500 autonomous mining vehicles
worldwide to over 1000 in this timespan.
This has been aided by the continued development of sensors,
perception algorithms, and communication networks. These vehicles
use an array of sensors, including cameras, radar, and LiDAR of
different wavelengths, in order to function in all light and
weather conditions – these must all be ruggedized to withstand the
harsh mining environments. Perception algorithms help detect
hazards in a vehicle's path and minimize the impact of dust and
humidity, which are commonplace in mines, on autonomous operation.
Finally, the establishment of robust 5G networks on-site enables
communication between vehicles and further improves safety.
The new IDTechEx report "Electric Vehicles in Mining 2024-2044:
Technologies, Players, and Forecasts" provides more analysis
of the technologies that will revolutionize the mining industry,
financial analysis of mining EVs, and case studies of key players
across the EV supply chain.
To find out more about this IDTechEx report, including
downloadable sample pages, please visit
www.IDTechEx.com/EVMining.
For the full portfolio of electric vehicles market research from
IDTechEx, please visit www.IDTechEx.com/Research/EV
About IDTechEx:
IDTechEx provides trusted independent research on emerging
technologies and their markets. Since 1999, we have been
helping our clients to understand new technologies, their supply
chains, market requirements, opportunities and forecasts. For more
information, contact research@IDTechEx.com or
visit www.IDTechEx.com.
Images download:
https://www.dropbox.com/scl/fo/1dgjy4ewh1xxv3d440v95/AD0_z3_PkIE3HVM9Q10feHg?rlkey=u8c93pac7ixrtmqp30xu4n2yv&dl=0
Media Contact:
Lucy Rogers
Sales and Marketing Administrator
press@IDTechEx.com
+44(0)1223 812300
Social Media Links:
Twitter: www.twitter.com/IDTechEx
LinkedIn: www.linkedin.com/company/IDTechEx
Photo:
https://mma.prnewswire.com/media/2419377/IDTechEx_Mining_Vehicles_Infographic.jpg
Logo: https://mma.prnewswire.com/media/478371/IDTechEx_Logo.jpg
View original
content:https://www.prnewswire.co.uk/news-releases/idtechexs-three-technologies-that-will-revolutionize-mining-vehicles-302153050.html